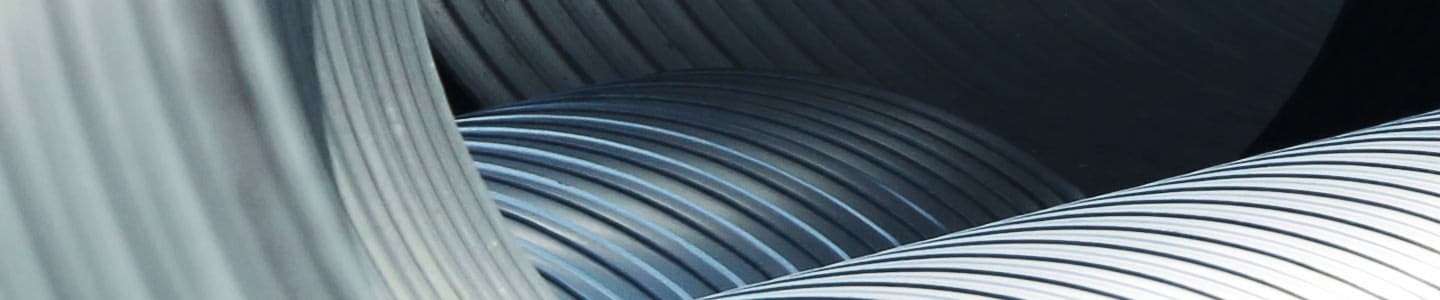
OSHA Warehouse Checklist
July 17, 2024
OSHA Warehouse Checklist
Introducing Stronghold® Safety, renowned for its commitment to creating safer industrial environments through innovative solutions. Our expertise in safety management has made us a trusted partner for businesses seeking to enhance their operational safety across diverse sectors. In this discussion, we will highlight critical safety practices and standards that are essential for maintaining a secure and efficient warehouse. Join us as we navigate the complexities of warehouse safety, providing insights and strategies that aim to elevate your safety protocols.
Warehouse safety is an integral part of industrial operations, often overlooked until it is too late. The Occupational Safety and Health Administration (OSHA) provides stringent guidelines and regulations specifically designed to maintain safety standards and protect workers in warehouse environments. These standards are not just about compliance; they are about creating a workplace where safety is woven into every activity and decision. As you read through this article, you will gain a deeper understanding of why a comprehensive warehouse safety checklist is not only a regulatory requirement but a crucial component of operational success.
History of Warehouse Safety Regulations
The journey towards today’s warehouse safety standards began in 1970 with the establishment of OSHA. The agency was created in response to rising workplace accidents and the growing need for a comprehensive approach to occupational safety. Prior to OSHA’s inception, there were few standardized safety measures in place, leaving workers vulnerable to numerous hazards inherent to industrial work environments.
Over the decades, OSHA has played a pivotal role in transforming workplace safety, specifically within the warehousing sector. Through the development of detailed regulations and guidelines, OSHA has helped mitigate risks associated with heavy equipment, hazardous materials, and other common warehouse safety hazards. The evolution of these regulations reflects an ongoing commitment to reducing workplace injuries and fatalities, showcasing a dynamic approach to occupational safety that adapts to technological advancements and changing industry practices.
This historical commitment to safety is crucial as it sets the foundation for the detailed safety measures we implement today. As we delve deeper into the specifics of warehouse safety, it's important to understand that these regulations are not just bureaucratic necessities but lifesaving measures refined over years of experience and expert input.
Why Warehouse Safety is Critical
Ensuring a safe warehouse environment is pivotal, not just for meeting regulatory requirements but for safeguarding the well-being of every individual stepping into the facility. Each year, accidents in warehouses result in numerous injuries and fatalities that could have been prevented with proper safety measures and awareness. The human cost of neglecting safety protocols is immense, affecting not only the injured but also their families and coworkers. Moreover, accidents disrupt operations, leading to significant financial losses through damaged goods, equipment repairs, and potential legal liabilities.
Warehouse safety extends beyond preventing injuries; it's about creating a systematic approach to maintain high productivity and morale among workers. Employees who feel safe are more likely to be engaged with their work, contributing to overall operational efficiency. Safety is also critical in maintaining a company's reputation. Frequent accidents can tarnish your brand and make it difficult to attract quality talent or retain clients.
From a practical standpoint, a safe warehouse is organized and efficient. Clear safety protocols contribute to smoother operations, where everyone understands their role and the measures in place to protect them. This environment not only reduces the likelihood of accidents but also boosts confidence among employees, enabling them to perform their duties effectively without undue concern for their personal safety.
In essence, warehouse safety is a key component of operational success. It involves every aspect of the warehouse operations—from the daily handling of equipment to the strategic implementation of safety audits and training programs. As you continue to read, remember that the goal of enhancing safety is not merely about compliance but about fostering a culture where safety is a priority. Each component of the warehouse safety checklist you'll learn about is designed to support this culture, ensuring that every precaution is taken to protect the workers who are the backbone of your operations.
Common Warehouse Safety Hazards
In any warehouse, certain hazards are more prevalent and pose significant risks to the safety and health of employees. Understanding these common warehouse safety hazards is the first step towards mitigating them effectively. Here’s a breakdown of the key dangers and the best practices to avoid them:
Forklift Accidents
Forklifts are indispensable in the daily operations of a warehouse but are also a leading cause of injury. Accidents typically occur due to improper handling, lack of training, or mechanical failures. To prevent these incidents, it's crucial to ensure that all forklift operators are adequately trained and certified. Regular maintenance and inspections of forklifts should be a non-negotiable part of your safety protocol, alongside clear guidelines on speed limits and load capacities within the warehouse.
Slips, Trips, and Falls
These are among the most common incidents in warehouse settings, often resulting from wet floors, uneven surfaces, or cluttered walkways. The key to preventing these accidents is maintaining clean and clear pathways, ensuring all spills are promptly cleaned up, and that safety signs are visible around wet areas. Employing non-slip floor mats and maintaining good lighting can also significantly reduce the risk of falls.
Hazardous Chemicals
Handling and storing hazardous materials improperly can lead to severe health risks and accidents. Compliance with OSHA’s Hazard Communication Standard is essential, which includes maintaining proper labeling of all chemicals, providing Material Safety Data Sheets (MSDS) to all employees, and training workers on the procedures for handling these substances safely. Adequate ventilation systems and appropriate personal protective equipment (PPE) are also critical to ensuring the safety of those who work with or around hazardous materials.
Heavy Equipment
Apart from forklifts, other heavy equipment like pallet jacks and hoists are commonly used in warehouses. The primary safety measure here is proper training for all operators and regular equipment checks. It's also important to enforce safety zones where only authorized personnel can enter, especially when heavy equipment is in operation.
Machine Entanglement
Machinery with moving parts can pose entanglement hazards, particularly if safety guards are missing or malfunctioning. To prevent accidents, regular inspections and maintenance of machinery to ensure all safety guards are in place and functional are necessary. Additionally, training employees to wear close-fitting clothing and to keep hair and jewelry secured can reduce the risk of entanglement.
Addressing these common hazards with diligent preventive measures and ongoing employee education forms the backbone of a robust warehouse safety checklist. Each of these areas requires specific attention and protocols, which not only comply with OSHA regulations but also contribute to a safer and more efficient workspace.
OSHA Standards for Warehouses
Adherence to OSHA standards is not just about legal compliance; it’s about building a safety culture that enhances productivity and preserves the health of your workforce. Here’s an overview of key OSHA standards that directly impact warehouse operations and the safety measures you can implement:
Forklift Safety
OSHA's guidelines for forklifts cover everything from operator training to daily inspection routines. It's essential that forklift operators receive certified training and undergo periodic evaluations to ensure they continue to operate vehicles safely. Additionally, warehouses should establish and enforce strict protocols for forklift maintenance to ensure these machines are in safe working condition at all times.
Hazard Communication
The Hazard Communication Standard is designed to protect employees from hazardous chemicals. Under this standard, it’s crucial that all hazardous chemicals in the warehouse are properly labeled and that safety data sheets are available and accessible to all employees. Furthermore, regular training sessions must be conducted to educate employees on the risks associated with these chemicals and on proper handling procedures.
Electrical Safety
OSHA’s electrical standards are designed to protect employees from electrical hazards such as shock, fire, and explosion. Ensuring all wiring methods are up to code and that circuit protection devices are in place is fundamental. Regular inspections should be conducted to identify and remedy potential electrical hazards before they lead to accidents.
Exit Routes
Warehouses must have clearly marked, unobstructed exit routes to ensure safe evacuation in case of emergencies. Regular checks are necessary to ensure that all exits are accessible and that emergency lighting is functional. OSHA requires that exit routes be continuously maintained free of equipment, materials, and debris.
Mechanical Power Transmission
For machinery that transmits energy (e.g., belts, pulleys, chains), OSHA mandates the use of guards to prevent worker injuries. Regular inspections should ensure these guards are intact and functioning. Training employees on the risks associated with mechanical power transmission and the importance of reporting any issues immediately is also vital.
Respiratory Protection
In environments where airborne hazards are present, OSHA requires the implementation of a respiratory protection program. This includes selecting the correct respirators, providing fit testing and training for employees, and conducting regular evaluations of the program to ensure ongoing effectiveness.
Lockout/Tagout Procedures
To prevent accidental machine start-up or the release of stored energy, OSHA’s lockout/tagout procedures must be strictly followed. This involves training authorized employees on correct lockout/tagout practices, using appropriate lockout devices, and conducting regular audits to ensure compliance.
Portable Fire Extinguishers
OSHA requires that all workplaces, including warehouses, be equipped with suitable fire extinguishers and that employees are trained on their proper use. Regular maintenance and inspection of these extinguishers are also necessary to ensure they are operational when needed.
By integrating these OSHA standards into your daily operations, you not only ensure compliance but also foster a safety-first mindset among your employees. Next, we'll discuss how to create a comprehensive warehouse safety checklist that encompasses all these elements and more, to keep your operations running smoothly and safely.
Creating a Comprehensive Warehouse Safety Checklist
To ensure that all aspects of warehouse safety are regularly checked and maintained, developing a comprehensive warehouse safety checklist is essential. This checklist serves as a fundamental tool for managing and auditing the safety practices within your warehouse. Here’s how to structure your checklist to cover all necessary safety checks:
General Safety Checks
Begin with a thorough inspection of the building and its surroundings for any structural damage or obstructions that could pose risks. Check for proper signage, secure storage systems, and clear pathways. Ensure all safety measures are visible and accessible.
Fire Safety
Fire safety checks are crucial. Inspect all fire extinguishers, alarms, sprinkler systems, and emergency exits to ensure they are in working order and meet local fire codes. Regular drills should also be part of your checklist to practice evacuation procedures.
Ventilation
Proper ventilation is essential, especially in areas where chemicals are stored or where machinery is operated. Check that ventilation systems are functioning correctly and are capable of removing harmful fumes and dust from the work environment.
Lighting
Adequate lighting helps prevent accidents by improving visibility. Ensure that all areas of the warehouse, particularly where detailed work or machinery operation occurs, are well-lit. Regularly check and replace any faulty lighting fixtures.
Cleanliness and Hygiene
Maintain cleanliness to prevent slips, trips, and falls. Ensure that all areas are free of debris, spills are cleaned up immediately, and waste bins are accessible and emptied regularly. Hygiene stations should also be maintained to promote health among the workforce.
Hazardous Material Handling
For warehouses that store or use hazardous materials, your checklist should include protocols for proper labeling, storage, and handling. Ensure all containers are intact and labels are clear, and that all employees handling these materials are trained in proper procedures.
Equipment Maintenance
Regular inspection and maintenance of all warehouse equipment prevent malfunctions and accidents. Include checks for mechanical integrity, proper function, and safety compliance for all tools and machinery used in the warehouse.
Personal Protective Equipment (PPE)
Ensure that appropriate personal protective equipment is available and in good condition. Check that all employees have access to and are using the correct PPE for their tasks.
Training and Communication
Regular training sessions and clear, accessible communication channels are key to maintaining a safe working environment. Include checks for up-to-date training records and ensure that all new and existing employees are familiar with the warehouse’s safety procedures.
Regular Safety Audits
To keep your safety standards current, regular internal and external safety audits are essential. These audits help identify areas of improvement, reinforce safety protocols, and ensure compliance with the latest OSHA standards. The checklist should include a schedule for these audits and protocols for addressing any issues they uncover.
Conducting Regular Safety Audits
Conducting regular safety audits is a crucial component of maintaining a safe warehouse environment. These audits serve as both a preventive measure and a method to continuously improve safety protocols. Here’s a detailed guide on how to perform these vital safety assessments:
Steps for Performing Internal Safety Audits
Preparation: Gather all necessary safety documentation, including previous audit reports, safety checklists, and employee training records. This step ensures you have a benchmark against which to measure current practices.
Inspection: Walk through the warehouse with your safety checklist, inspecting each area against set safety standards. Look for potential hazards, assess the condition of equipment and machinery, and observe operational practices.
Employee Feedback: Engage with employees during the audit to get direct feedback on the effectiveness of current safety measures and any concerns they might have. Employee insights are invaluable for identifying less obvious risks.
Report Findings: Document all findings from the audit, noting any deviations from safety standards and highlighting areas for improvement. This documentation is crucial for tracking progress over time and for regulatory compliance.
Action Plan: Develop an action plan to address any identified issues. This plan should include specific tasks, responsible parties, and deadlines for completion.
Follow-Up: Regular follow-up on the action plan is essential to ensure that all corrective measures are implemented effectively and in a timely manner. Repeat audits should check the status of these implementations.
Steps for External Safety Audits
External audits are conducted by third-party professionals who can provide an unbiased view of your warehouse’s safety standards.
Choosing an Auditor: Select a certified safety professional with experience in warehouse operations. This choice ensures that the auditor is familiar with industry-specific hazards and OSHA regulations.
Coordination: Work closely with the auditor to schedule the audit and provide them with all necessary documentation and access to your facilities.
Review of Findings: After the audit, review the findings with the auditor to gain a clear understanding of any issues. Ask for their recommendations on how to address these issues.
Implementation of Recommendations: Implement the auditor’s recommendations according to the priority and severity of the issues raised.
Certification and Compliance: Use the results of the external audit to ensure compliance with OSHA standards and to certify your warehouse as a safe working environment.
Regular internal and external safety audits are not just about compliance but about creating a proactive approach to warehouse safety. They help to identify potential hazards before they result in accidents, ensuring a safer workplace for everyone involved. By incorporating these audits into your regular operations, you uphold a high standard of safety, promote a culture of continuous improvement, and ultimately protect your most valuable asset—your employees.
Warehouse Safety Best Practices
Implementing warehouse safety best practices is essential to maintaining a safe working environment and ensuring compliance with OSHA regulations. Here are key strategies to enhance safety in your warehouse:
Regular Inspections
Continuous monitoring of the warehouse environment is crucial. Regular inspections help identify potential hazards before they lead to accidents. Ensure that these inspections are systematic and cover all aspects of the warehouse, including equipment, machinery, and work areas. Establish a routine schedule and stick to it, documenting all findings and corrective actions taken.
Up-to-Date Training
Training is a cornerstone of warehouse safety. All employees should be trained on the specific hazards of their job and the overall safety procedures of the warehouse. It’s important to keep this training up-to-date with any new regulations or changes in operations. Regular refresher courses ensure that safety remains at the forefront of every employee’s mind and practices.
Record Keeping
Maintain comprehensive records of all safety-related activities, including training sessions, inspections, audits, and incident reports. These records are not only crucial for regulatory compliance but also provide valuable insights into the effectiveness of your safety measures. They help track progress, identify trends in safety issues, and support continuous improvement efforts.
Clean Work Environment
A clean and organized warehouse significantly reduces the risk of accidents, such as slips, trips, and falls. Regular cleaning schedules, adequate storage practices, and clear labeling reduce clutter and ensure that hazards are minimized. This practice also extends to the proper disposal of waste and the regular maintenance of hygiene in communal areas, which helps prevent health-related issues among staff.
Effective Use of Safety Equipment
Ensure that all safety equipment, including personal protective equipment (PPE), fire extinguishers, and first aid kits, are accessible, properly maintained, and used correctly. Regular checks should be performed to ensure that this equipment is in good working order and that all employees know how to use it correctly in case of an emergency.
By embracing these best practices, you create a safer warehouse environment that not only protects your employees but also enhances operational efficiency and maintains compliance with important safety regulations. As you foster a culture of safety, remember that these practices are not static; they require ongoing attention and adaptation to new challenges and changes in the regulatory landscape.
Securing a Safer Tomorrow with Stronghold® Safety
With a comprehensive OSHA warehouse safety checklist in place, courtesy of Stronghold® Safety, you are well-equipped to tailor safety measures specifically to the needs of your warehouse environment. From ensuring the integrity of mechanical power transmissions to the meticulous management of hazardous materials, each component of the checklist plays a pivotal role in mitigating common warehouse hazards.
Remember, the safety of your employees is paramount, and adhering to these OSHA standards is not just about compliance—it's about actively protecting lives. Investing in the right safety practices, like regular safety audits and up-to-date training facilitated by Stronghold® Safety, leads to a safer and more productive work environment. Therefore, take the initiative to thoroughly assess your operational needs, consult with safety experts, and implement the most effective safety measures.
Safeguarding your warehouse is both a legal obligation and a moral responsibility, ensuring that every team member can return home safely at the end of each day. By leveraging the appropriate OSHA guidelines and tools provided by Stronghold® Safety, you create an environment that not only prevents accidents but also bolsters the well-being of your most valuable asset—your employees.
By integrating Stronghold® Safety into your workplace, you enhance overall safety, ensure compliance with regulations, and protect your employees from potential hazards. For a tailored approach to warehouse safety and to further refine safety solutions to meet your specific needs, reach out to Stronghold® Safety today. Our team is here to assist you in implementing robust safety measures that make a significant difference in protecting your workforce.