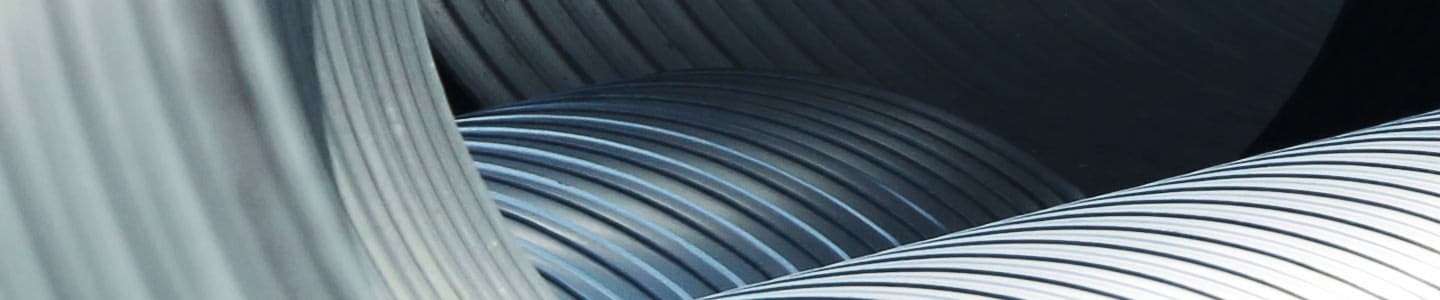
Implementing a Safety Culture: Steps to Engage Your Workforce
January 31, 2025
Implementing a Safety Culture: Steps to Engage Your Workforce
Creating a robust safety culture goes beyond simply implementing procedures; it requires embedding safety into the fabric of your organization's mindset and operations. At Stronghold Safety, our machine guarding assessments play a pivotal role in establishing a safety-focused workplace, where every employee is dedicated to maintaining safety standards. Below, we detail essential steps to enhance your safety culture by engaging your workforce through effective use of our assessments.
1. Educate & Inform
The Foundation of Safety Knowledge
Education is the cornerstone of a strong safety culture. Before employees can embrace safety measures, they must first understand their importance. Comprehensive Machine Guarding Assessments provide critical insights into potential hazards and specific challenges within your operations.
Safety Training Programs: Utilize assessment data to tailor training programs that directly address the specific risks identified in your facility. These sessions should be interactive, encouraging questions and hands-on demonstrations to solidify learning.
Continuous Education Initiatives: Offer regular refresher courses and safety updates to ensure employees remain aware of best practices and evolving safety standards. Providing access to online resources and safety bulletins can help reinforce ongoing learning.
Tools for Effective Training
Simulation Software: Use virtual tools and simulators to allow employees to practice and test their responses to potential safety scenarios in a controlled environment.
Multimedia Learning: Incorporate videos, tutorials, and interactive content in training sessions to make learning engaging and effective.
2. Promote Active Participation
Engagement through Involvement
An engaged workforce is key to maintaining continuous safety improvement. Inviting employees to participate in safety assessments ensures they have a voice in the safety process and fosters a sense of ownership over their work environment.
In-the-Field Observations: During Machine Guarding Assessments, include frontline employees in observational tours. They can provide essential insights into daily operations and practical constraints faced on the floor.
Feedback Mechanisms: Implement structured feedback loops, where employees can provide insights and suggestions based on their interaction with safety protocols. Regular safety meetings can serve as forums for feedback and discussion.
Creating Safety Ambassadors
Safety Champions Programs: Identify and empower safety champions within different departments to lead and promote safety initiatives.
Recognition for Contributions: Recognize and reward employees who actively contribute to improving workplace safety, thus encouraging a proactive approach.
3. Visible and Consistent Communication
Transparent Communication Channels
Clear communication is critical to instill the importance of safety and ensure everyone is on the same page. Regularly update your workforce about the results and actions stemming from Machine Guarding Assessments.
Safety Newsletters: Distribute electronic or printed newsletters that detail assessment findings, implemented changes, and safety tips.
Digital Display Boards: Use electronic boards around the facility to post daily safety reminders and important messages.
Building a Culture of Safety Dialogue
Open-Door Policies: Encourage an environment where employees feel comfortable bringing safety concerns to supervisors without fear of reprimand.
Regular Safety Huddles: Implement short daily or weekly meetings focused on safety updates, where supervisors can reinforce safe practices and address concerns.
4. Integrate Safety into Performance
Establishing Safety Accountability
Integrating safety into performance assessments underscores its importance within your organization. It emphasizes that safety is not a passive consideration but an active component of job roles.
Incorporate Safety Metrics: Include safety performance metrics in employee evaluations. Metrics may include adherence to safety protocols, incident reporting, and contributions to safety improvements.
Incentive Programs: Develop reward systems that recognize both individual and team achievements in maintaining high safety standards.
Aligning Safety Goals with Business Objectives
Safety as a Business Strategy: Highlight how safety excellence contributes to broader business goals, such as reducing downtime or enhancing product quality.
Cross-Departmental Collaboration: Encourage departments like HR, production, and maintenance to collaborate on setting and achieving shared safety goals.
5. Provide the Right Tools and Support
Resources for Safety Compliance
Ensuring your workforce is equipped with the necessary tools and resources is essential. Machine Guarding Assessments help identify the equipment and infrastructure needs to enhance your safety measures.
Updated Safety Equipment: Ensure that staff have access to up-to-date personal protective equipment (PPE) and tools, as recommended by assessment findings.
Dedicated Safety Budgets: Allocate specific budgets for ongoing safety improvements, ensuring that recommended upgrades from assessments are actionable.
Encouraging a Supportive Environment
Celebrating Compliance Milestones: Recognize and celebrate when your facility meets safety compliance milestones. This boosts morale and reinforces commitment to safety.
Management Support: Ensure open lines of communication between management and employees about safety needs, offering support and resources promptly when requested.
6. Continuous Improvement and Review
Iterative Enhancements to Safety Culture
Building a safety culture is an ongoing journey. Continually review and refine safety practices using feedback from Machine Guarding Assessments and active employee engagement.
Regular Reassessments: Schedule periodic Machine Guarding Assessments to evaluate the effectiveness of implemented safety measures and identify new areas of improvement.
Root Cause Analysis: After incidents or near-misses, conduct thorough analyses to understand root causes and take corrective actions to prevent future occurrences.
Incorporating Lean Safety Principles
Efficiency without Compromise: Establish safety protocols that enhance efficiency, using lean principles to eliminate waste while maintaining safety standards.
Safety Process Optimization: Align safety processes with operational workflows, ensuring they complement rather than hinder productivity.
Conclusion
Implementing a safety culture within your organization requires persistence, dedication, and the right tools. With Stronghold Safety’s Machine Guarding Assessments, you gain a comprehensive view of your operational safety needs, empowering you to create an engaging, responsive, and proactive safety environment. Encourage your workforce to take ownership of safety, integrate it into everyday activities, and witness the transformation into a resilient safety culture that supports both people and operations.